Arduino Spot Welder Car Battery Bundle Assembly Instructions
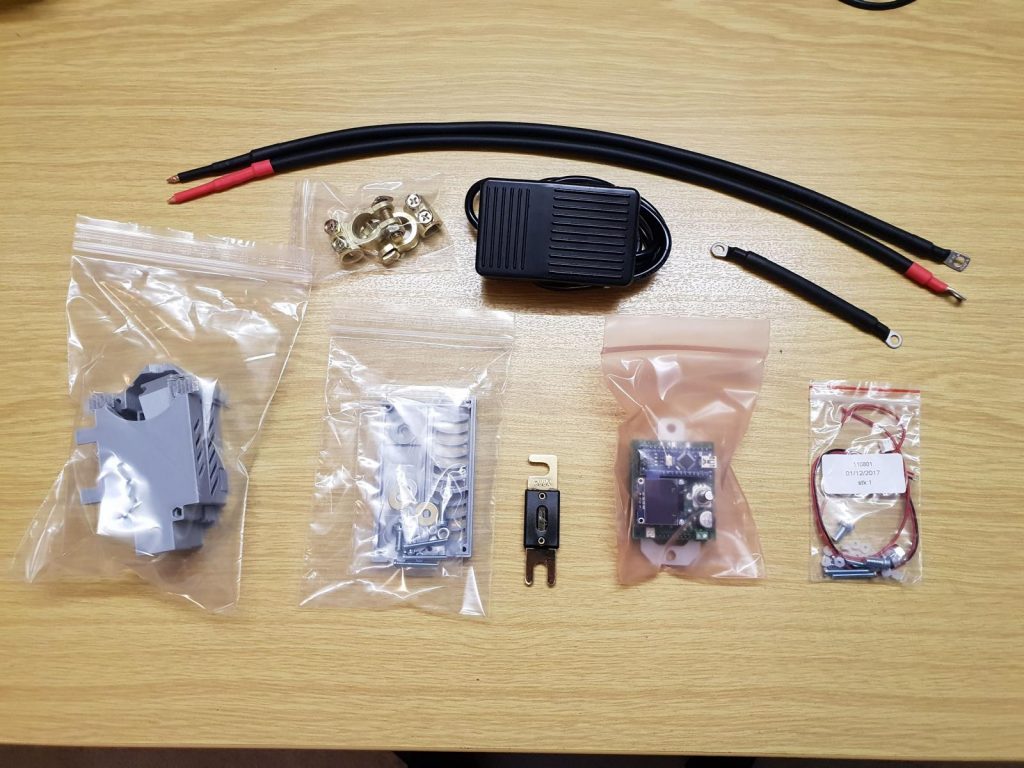
Assembly of the Prebuilt Kit
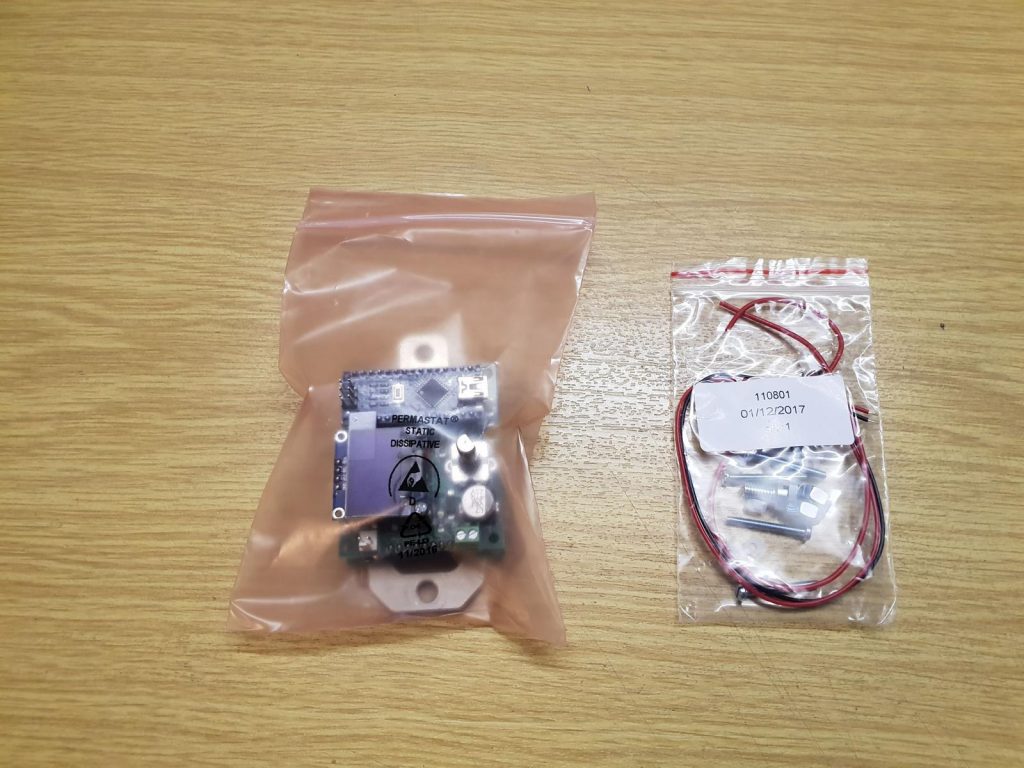
For this you will need the prebuilt kit and the little acessory bag that comes with it.
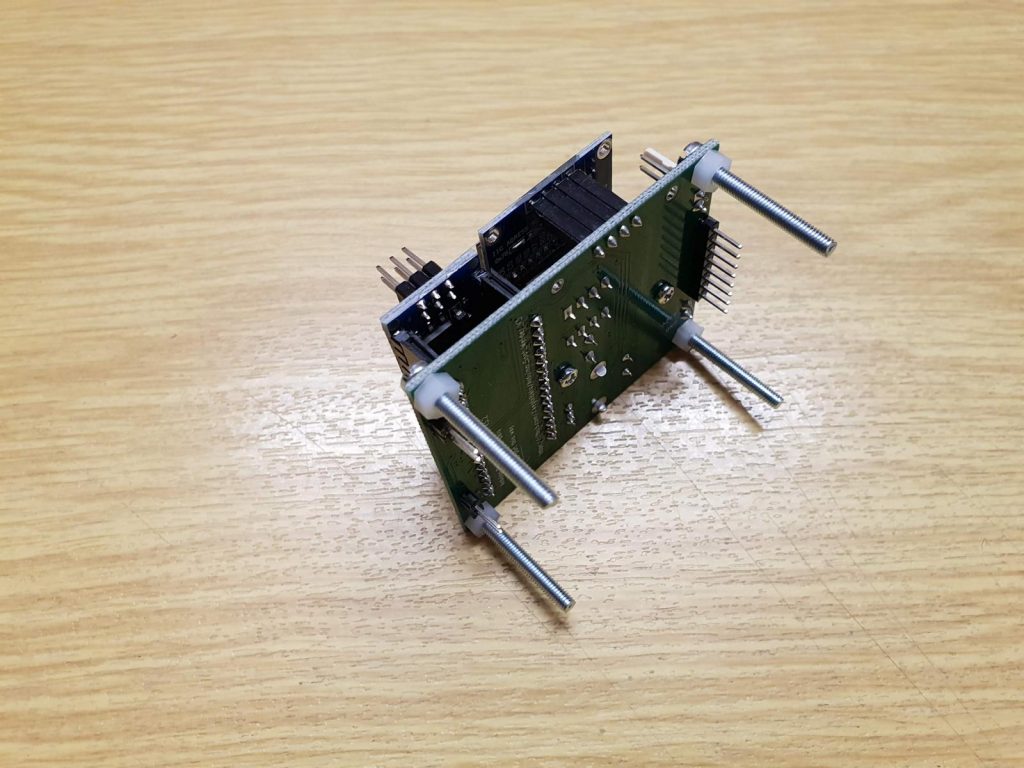
Seperate the two pcbs of the prebuilt kit and insert 4 M3x25 screws into the top pcb. Secure the screws with 4 M3 nylon nuts. Dont tighten the nuts to hard or they may break.
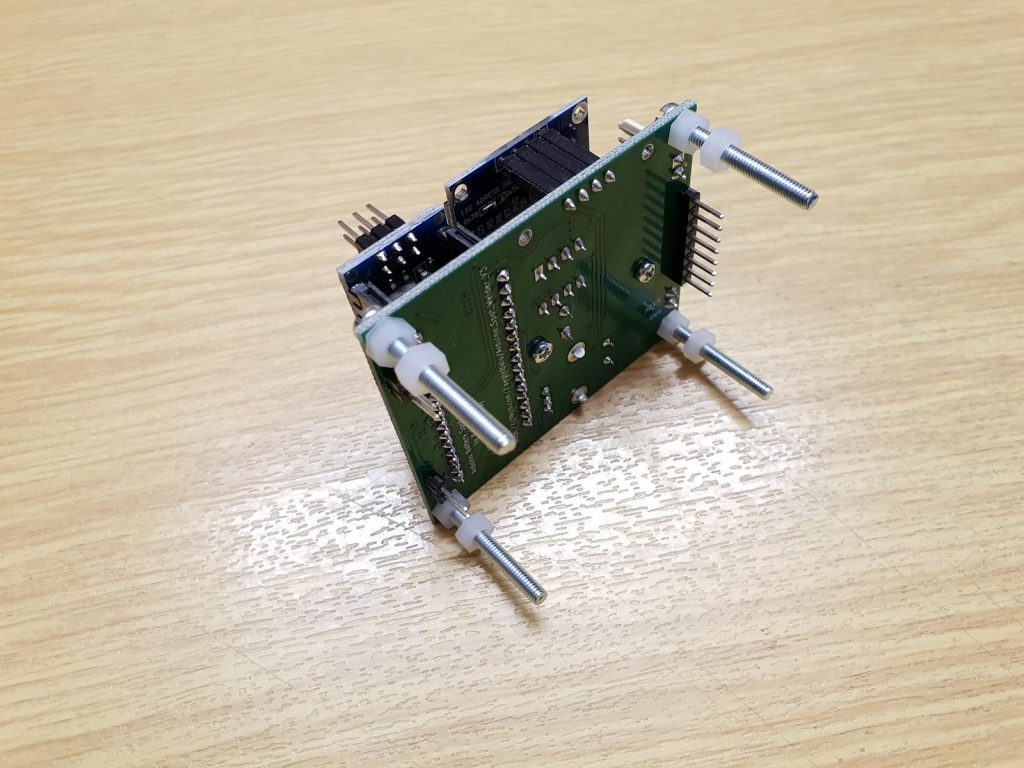
Screw 1 more nylon nut onto each of the M3x25 screws.
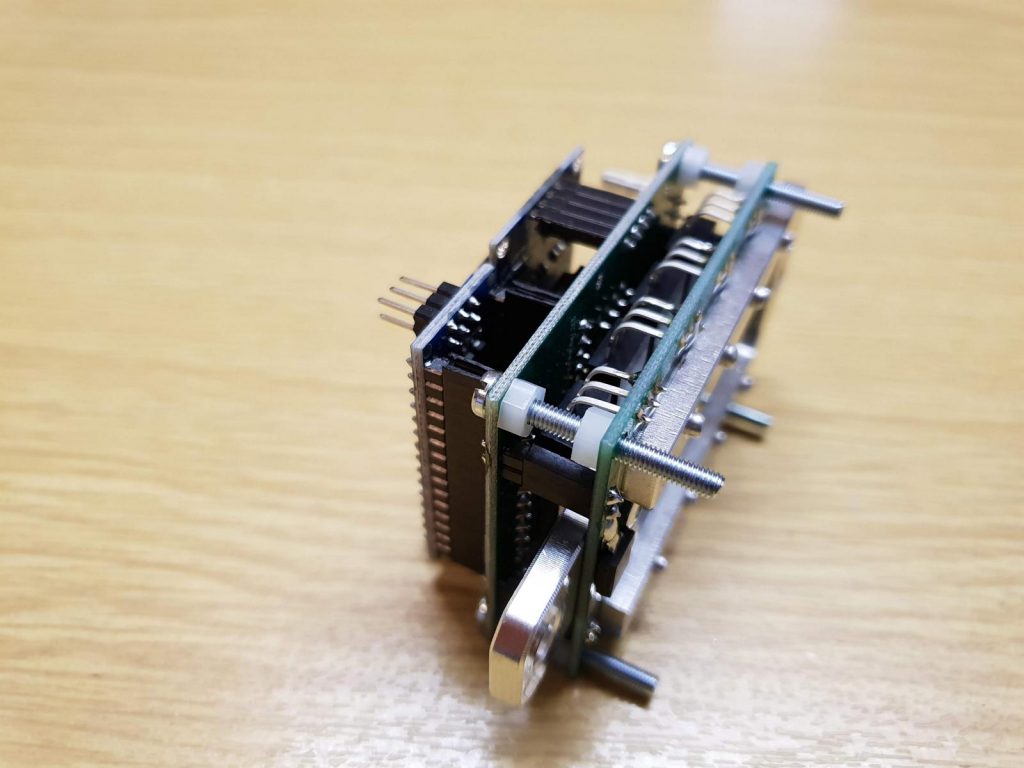
Stick the 2 pcbs back together and adjust the 4 nylon nuts so they sit flush against the bottom pcb.
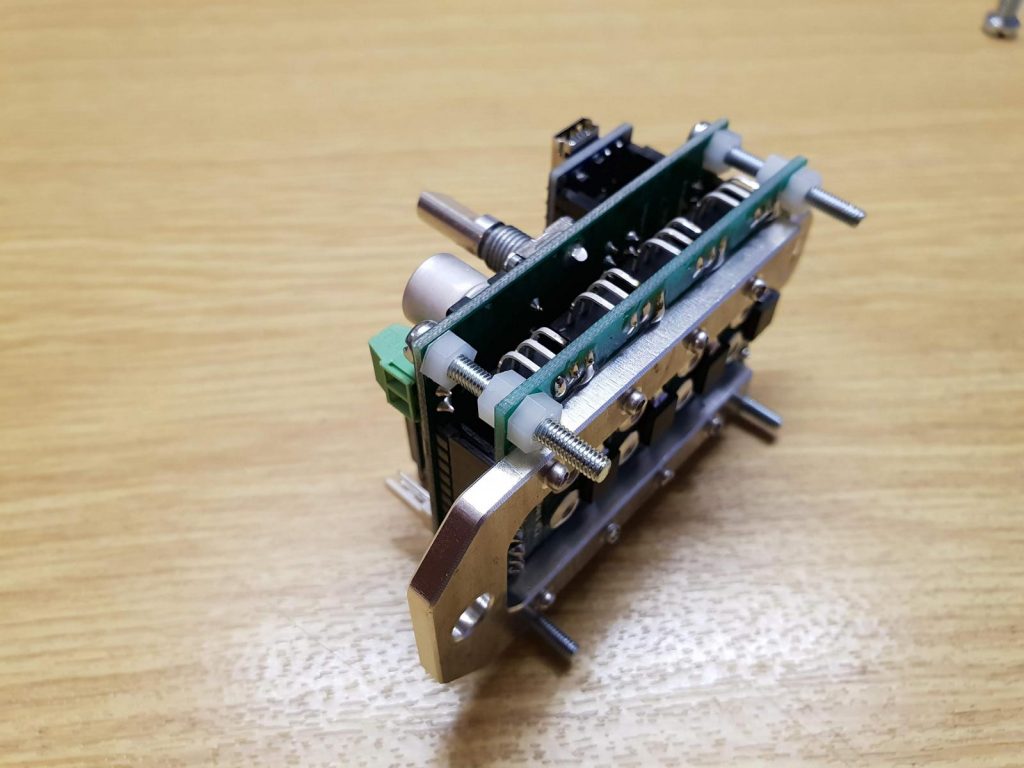
Ad one more nylon nut onto each screw to secure the bottom pcb (mosfet board) into place.
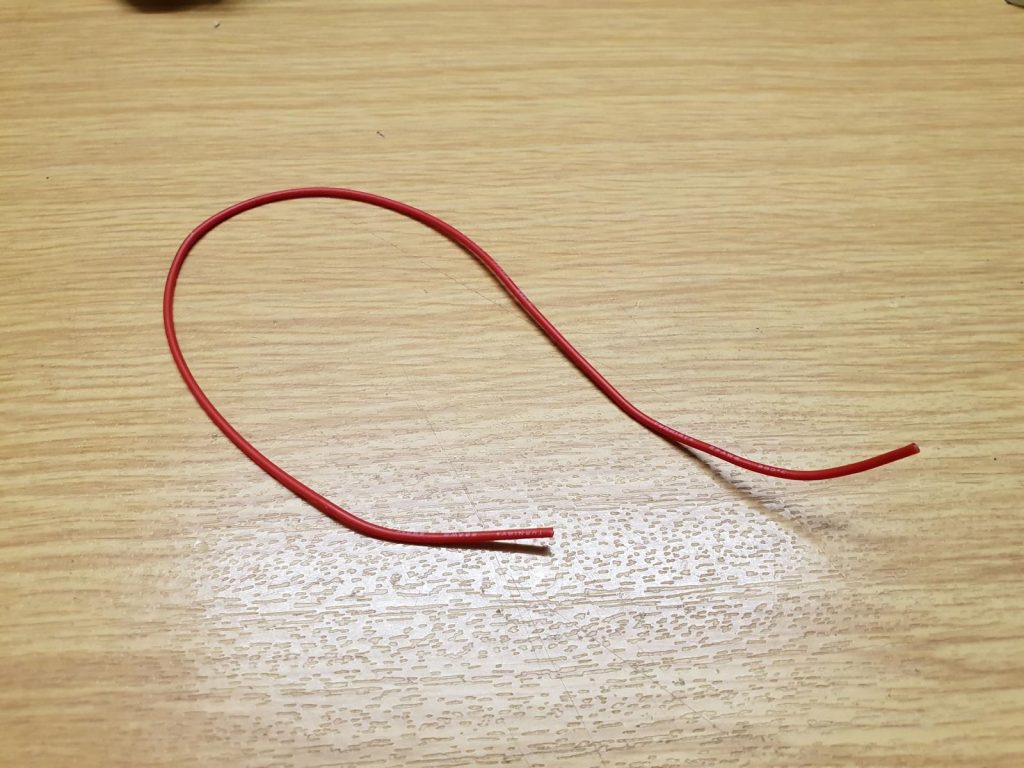
Next you need to prepare the red silicone cable that comes with the prebuilt kit.
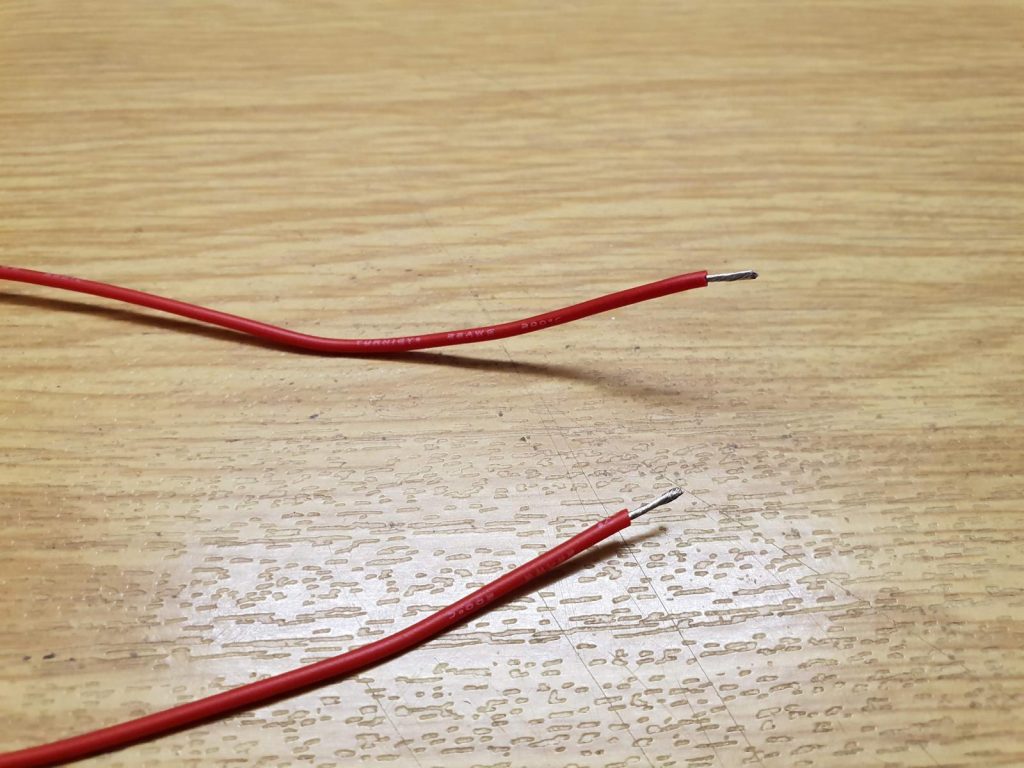
Remove about 5-7mm of the cable insulation from both ends
Prepairing the foot switch
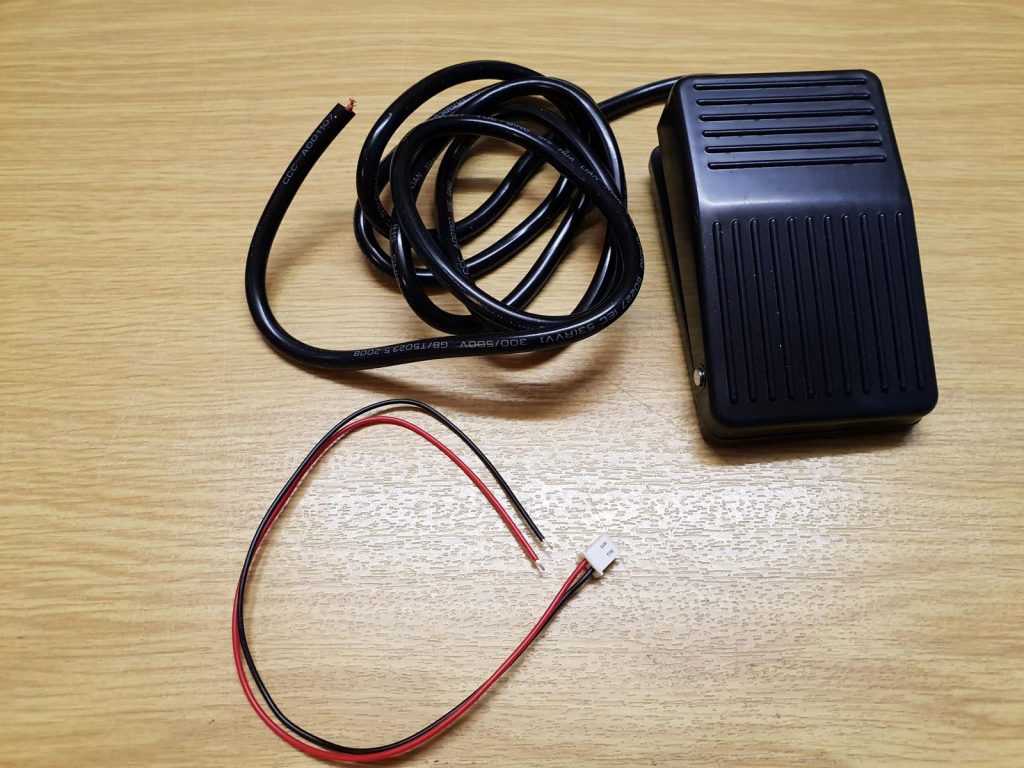
For this you need the foot switch and the cable with the white 2-pin connector from the prebuilt kits acessory bag.
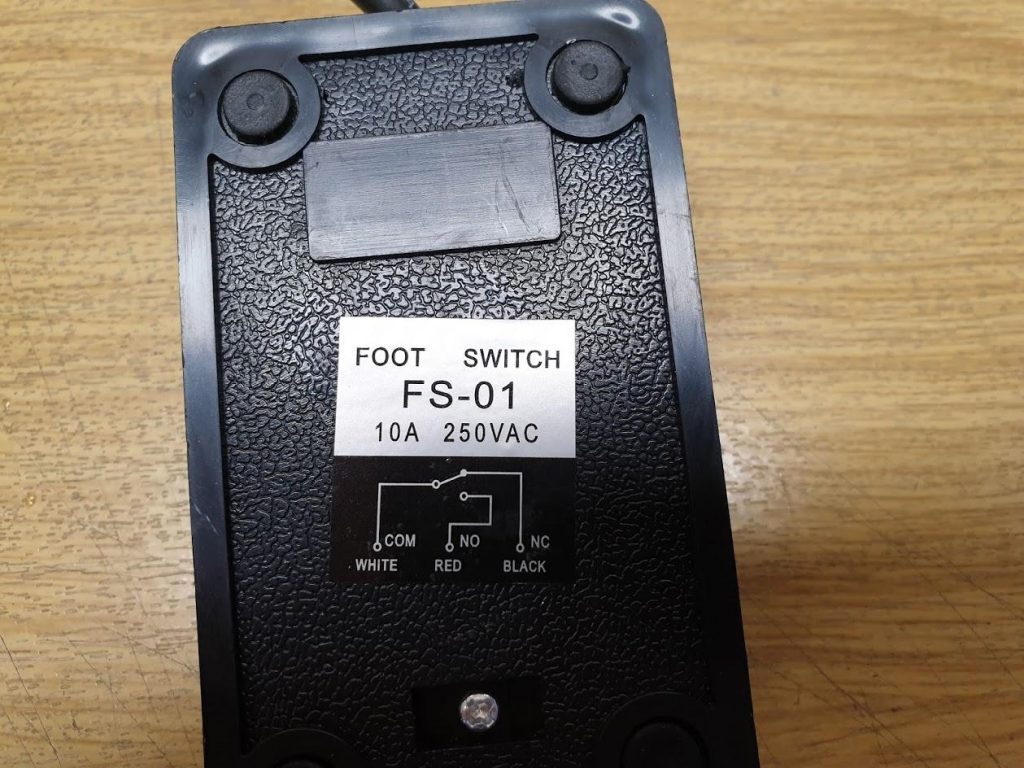
The foot switch needs to be operated in normally open (NO) configuration. This means it closes the contacts when it is pushed. Since the manufacturer of the foot switches tend to change cable colours pretty regulary you need to check first which colours are the correct ones to use.
To achieve this take a look on the back of the foot switch.There should be a sticker that shows the connections. For the foot switch on the picture you need to use the white and red cable.
But in another batch there might be foot switches that need the black and white cable to be operated in NO configuration.
Dont worry, you can not damage the welder by using the wrong cables. It will show you an error message if you use the wrong ones.
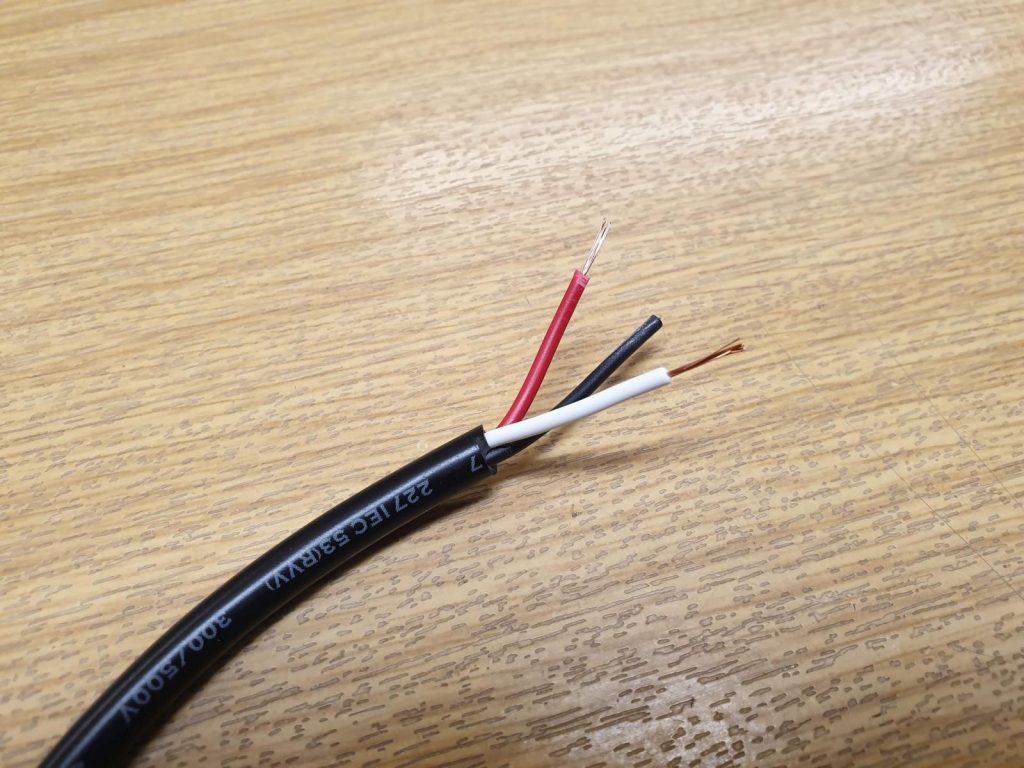
First remove about 4cm of the black isolation of the foot switch cable. Then remove about 1cm isolation from the cables ends.
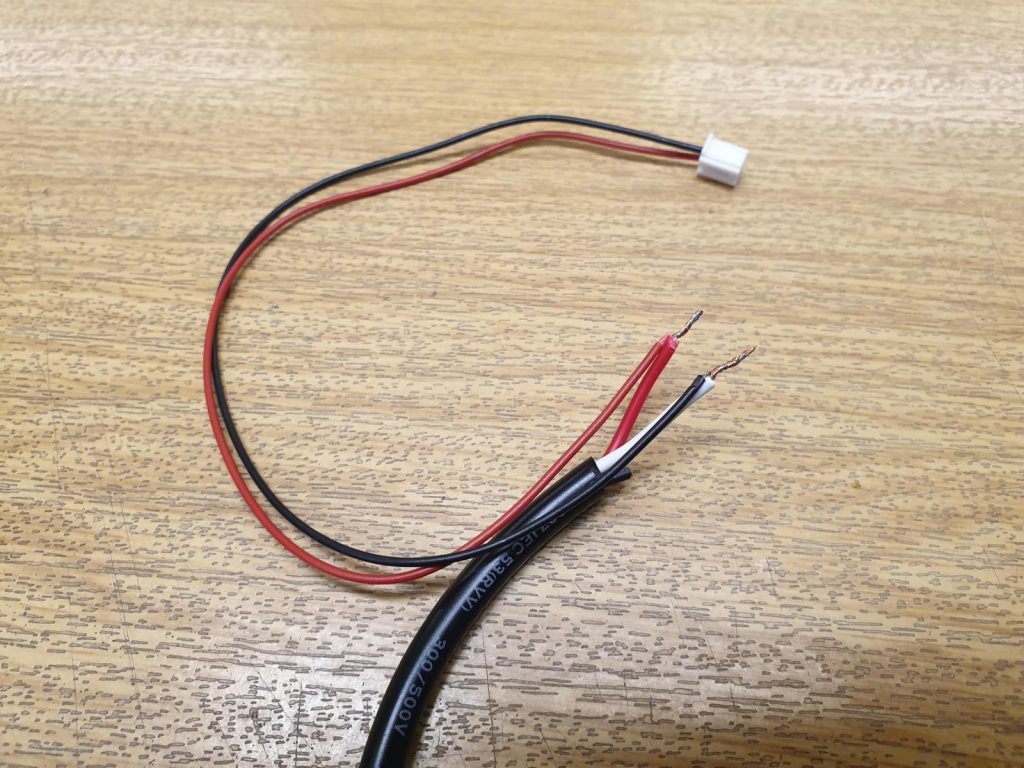
You can now simply solder the two cable ends to the cable with the white connector.
If you dont have a soldering iron remove about 1cm isolation from the cables with the white connector and twist them to the foot switch cables.
There is no polarity, so it doesnt matter if red goes to red and black to white or the other way arround.
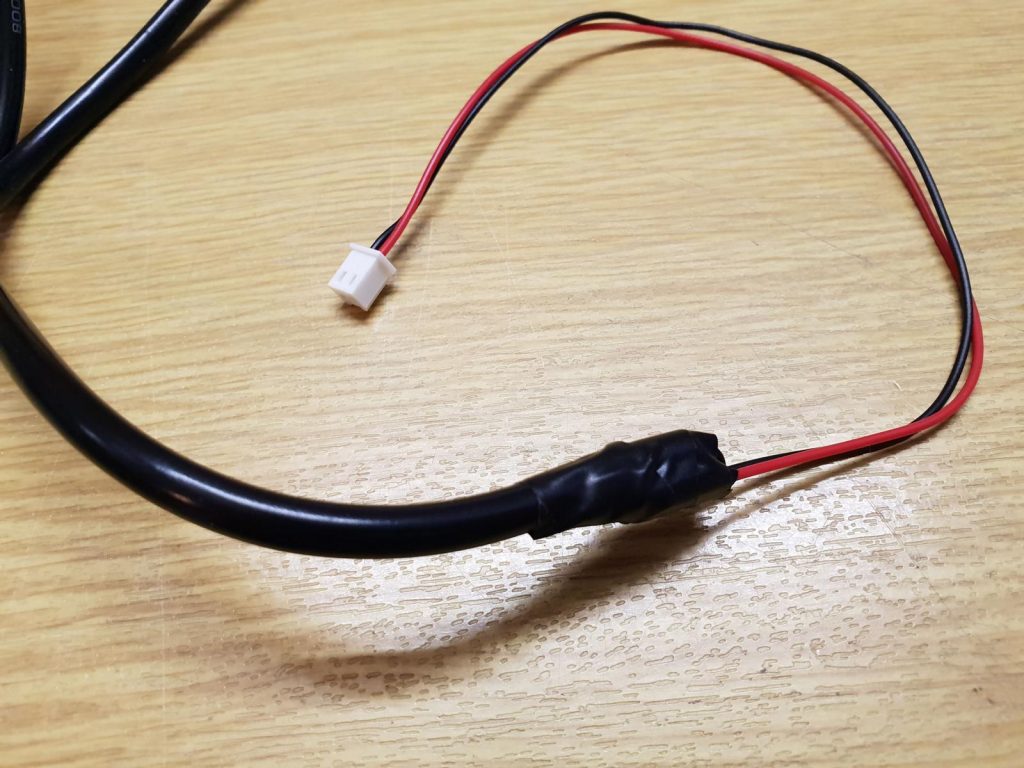
Isolate the connections with some electrical tape or shrink tube.
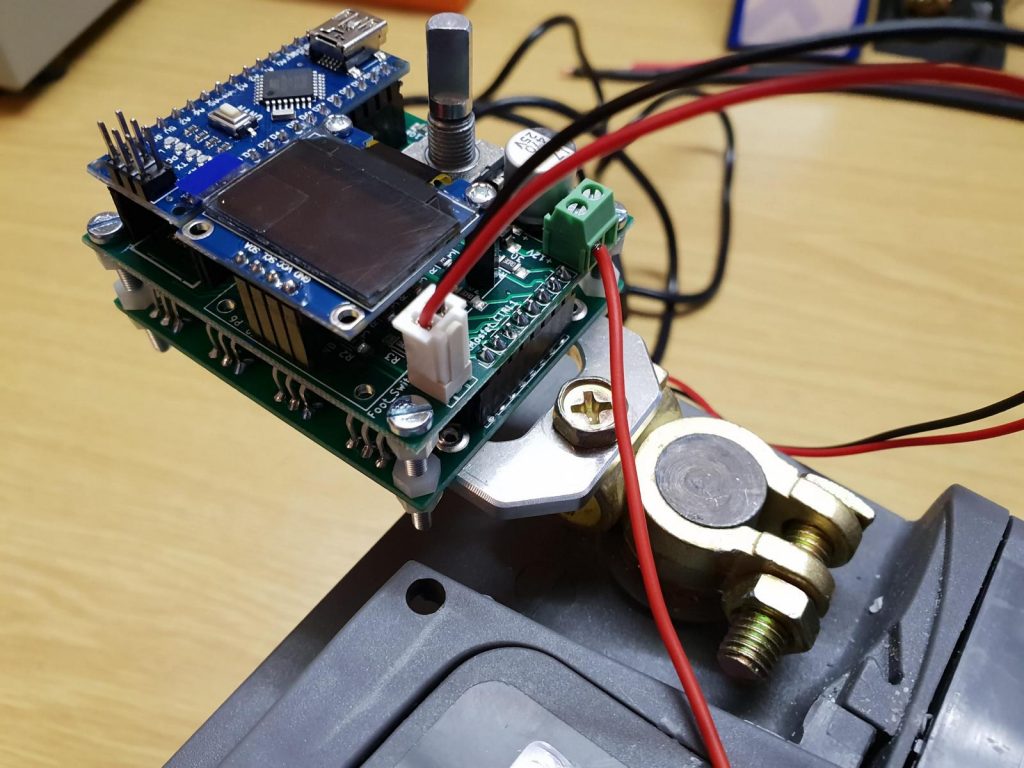
The socket for the foot switch is the white one on the spot welder pcb, you can see in the picture. It is also labeled “foot switch” on the pcb.
But dont connect the foot switch to the welder yet. It can be simply connected and disconnected after the assembly is finished.
Prepairing the case kit
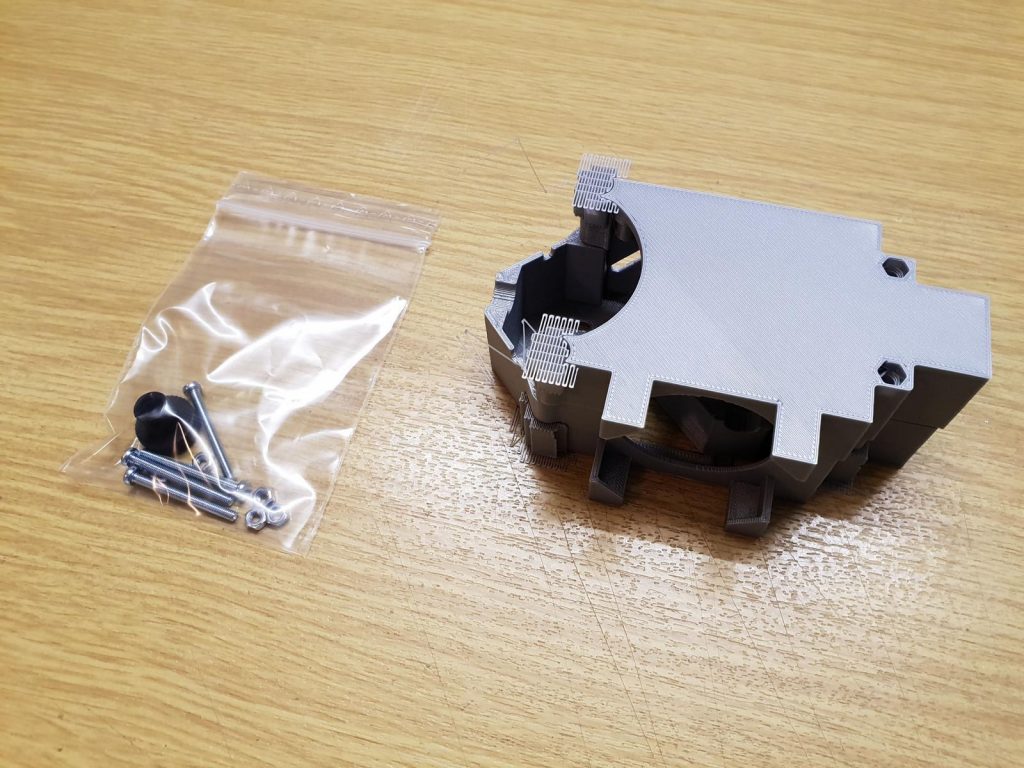
For this step you will need the case kit and its accessory bag.
Remove all the support material from the 3d printed parts. From the bottom part it usually can be easily removed by hand.
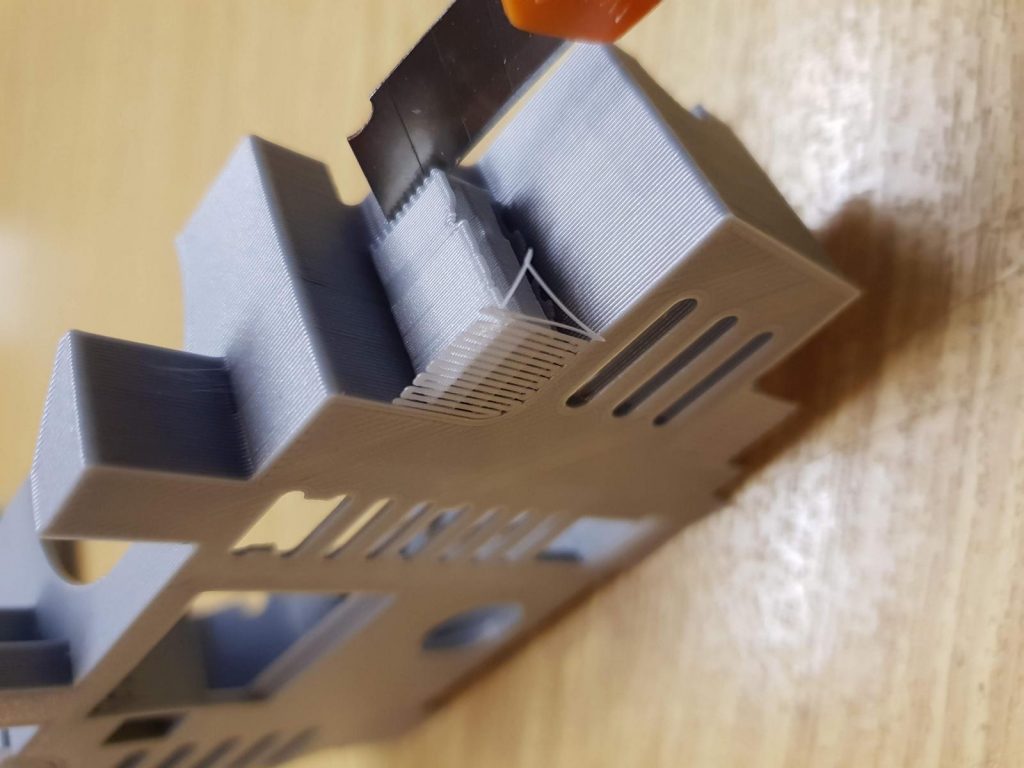
For the top part try to slice a knife between the 3d printed part and support material. The support will then easily break away.
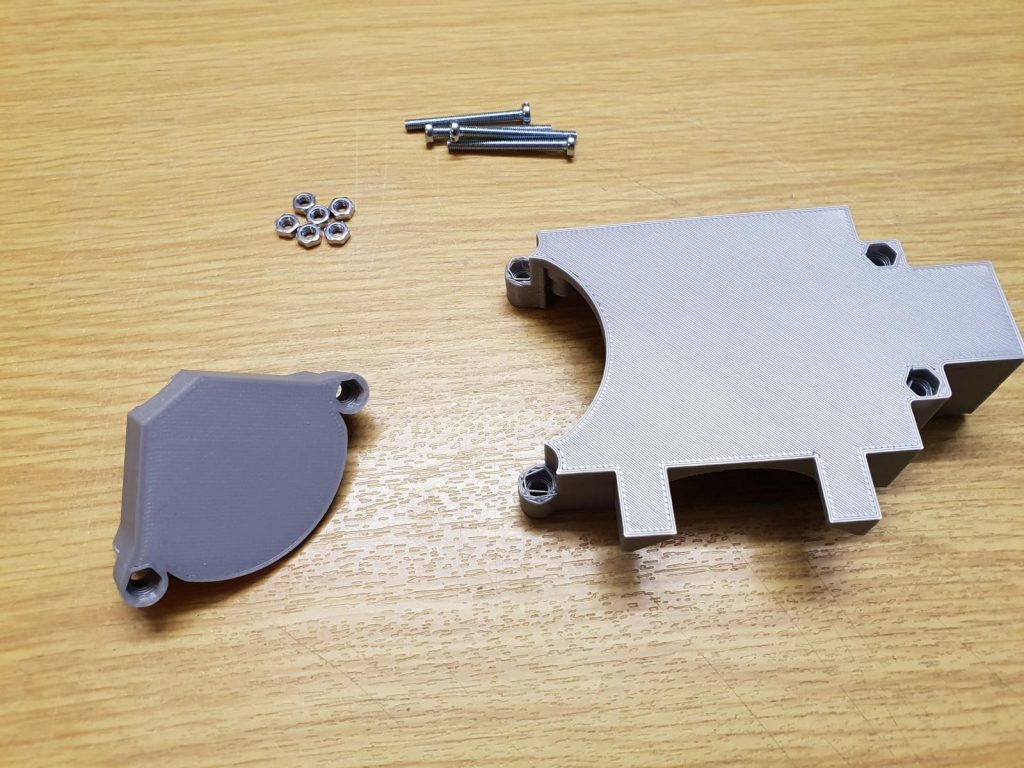
Now its time to insert the M3 nuts into the 3d printed parts.
Stick a M3 screw through the hole and screw on a M3 nut.
Tighten the screw to pull the nut into its pocket. Make sure the nut is aligned properly to the pocket when pulling it in.
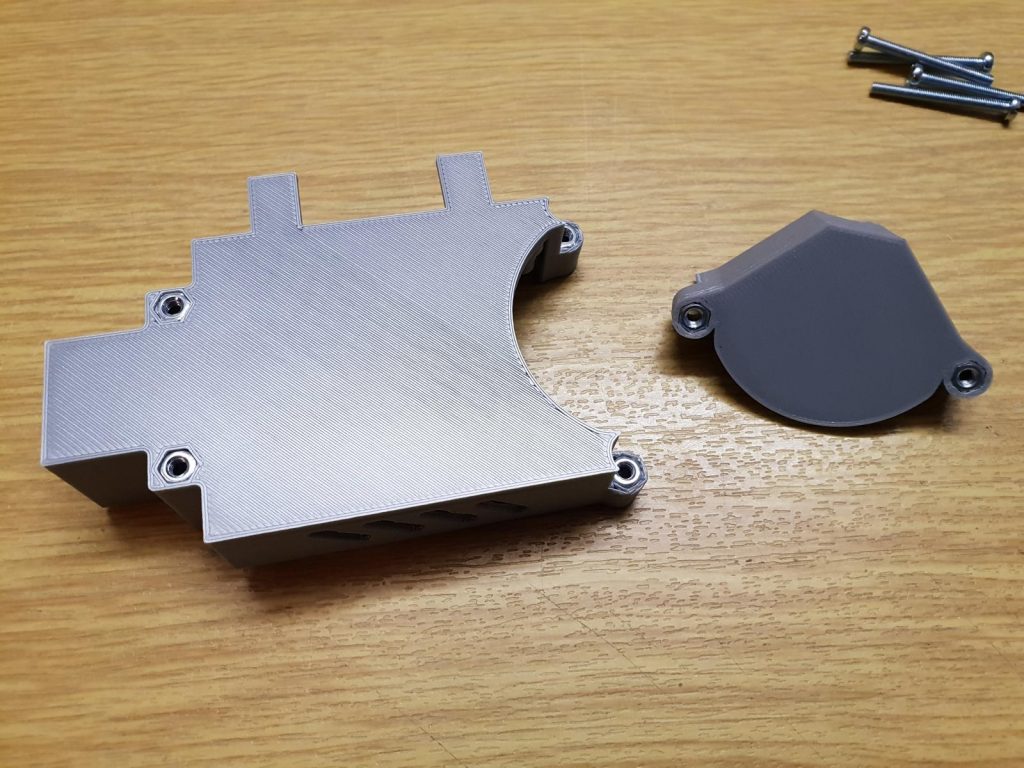
Repeat for all 6 M3 nuts.
Mounting the prebuilt kit in the case
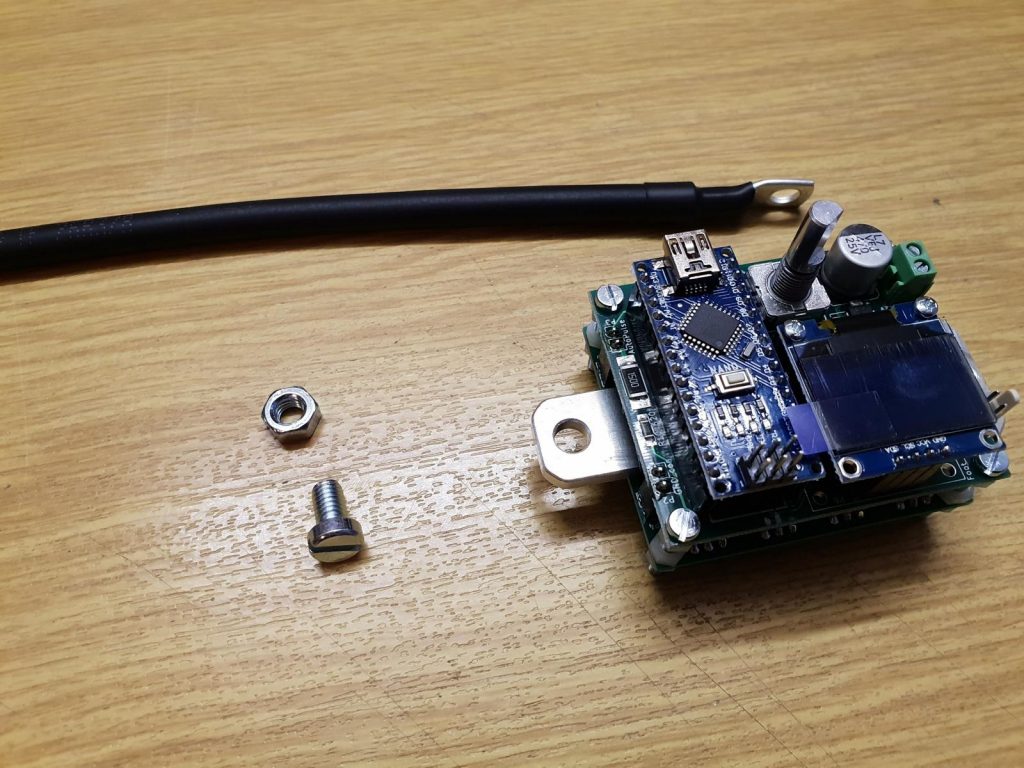
Take the prebuilt kit, the negative welding cable and one M6 screw with M6 nut
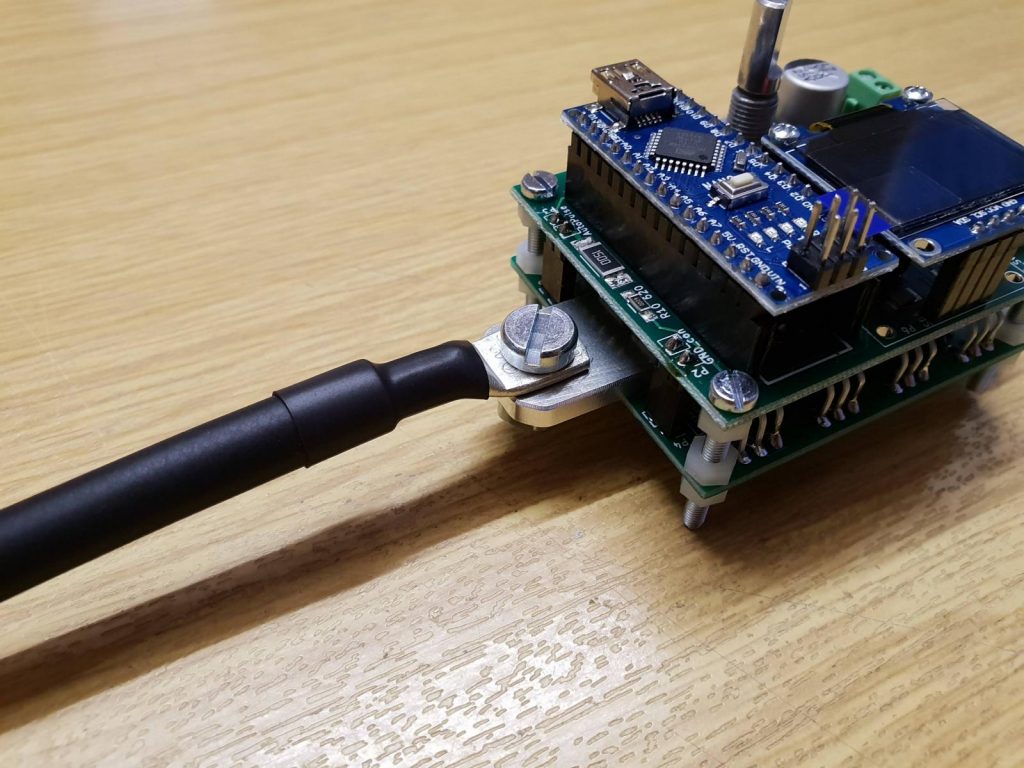
Screw the negative welding cable to the straight aluminium part.
It is very important to screw it to the straight aluminium part NOT TO THE U-SHAPED one.
Make sure you strongly tighten the M6 nut, to guarantee a good electrical connection between the welding cable and the aluminium part.
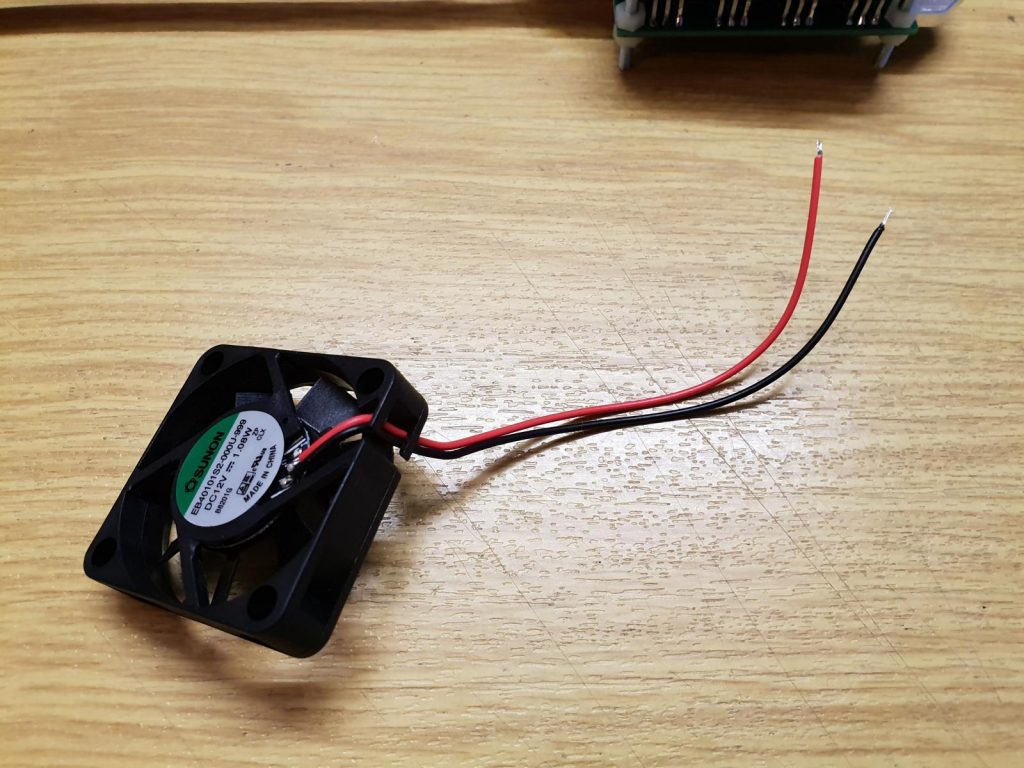
Shorten the wires from the case fan to about 10cm and remove a bit of the insulation from the ends.
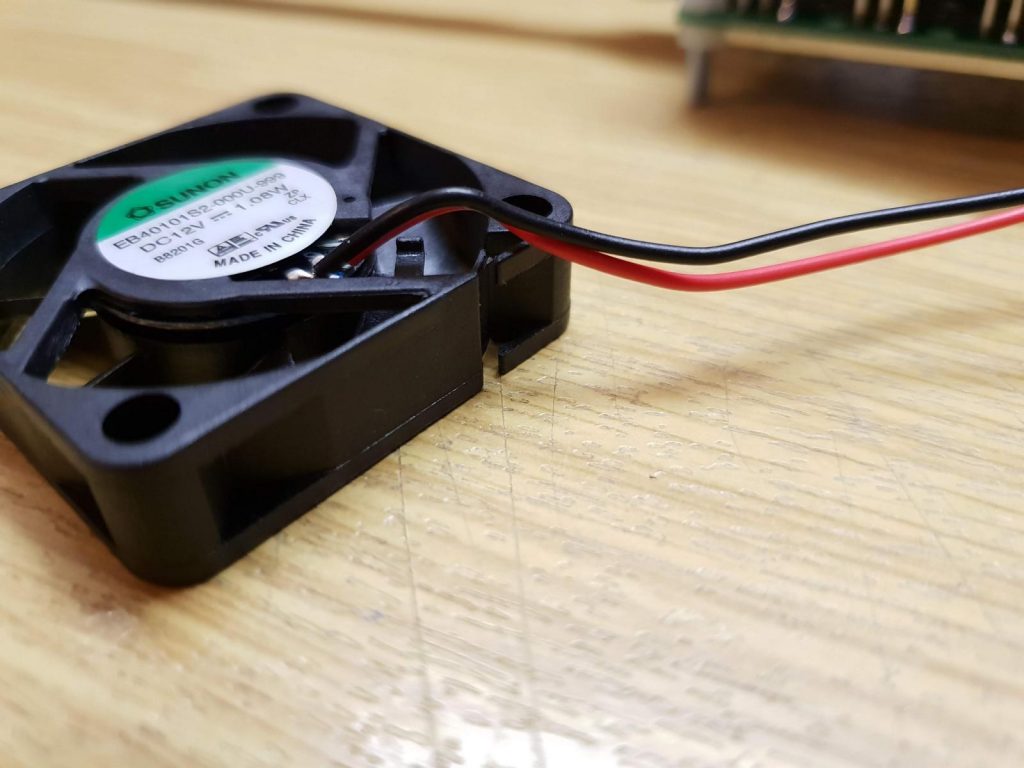
Remove the wires from the groove in the case fan.
From now on be carefull to not break off the wires from their soldering spot on the fans pcb.
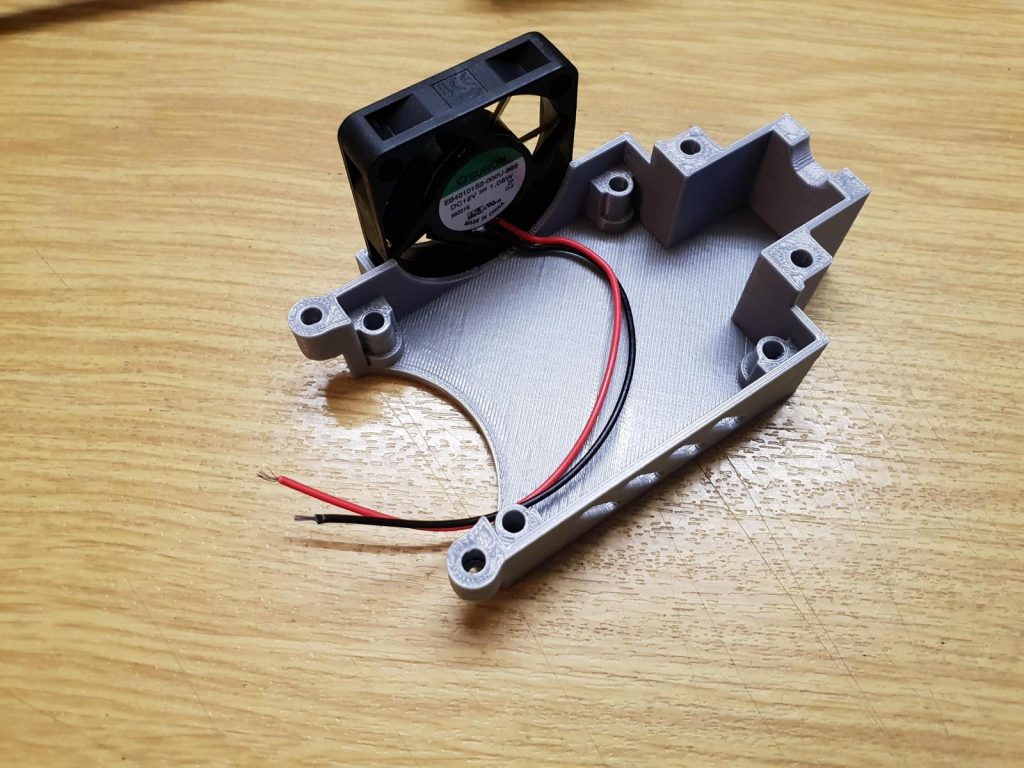
Seat the fan in its holder in the buttom part of the case kit. The sticker on the fan should face inside the case, so the fan later blows fresh air inside the case.
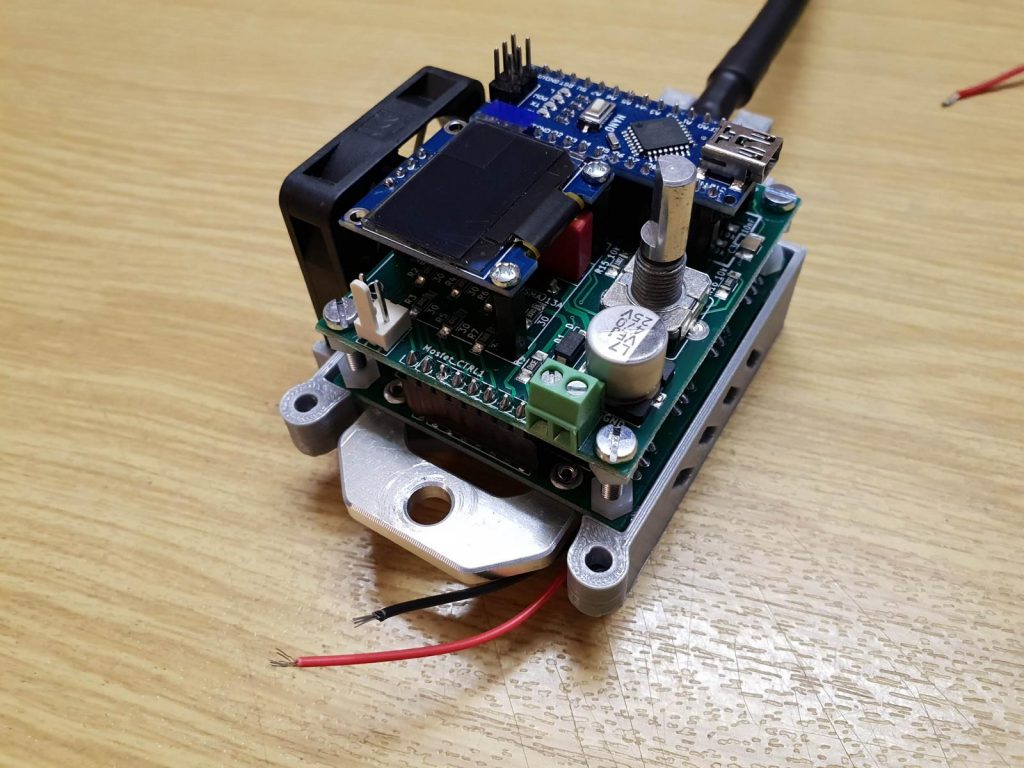
Seat the prebuilt kit into the case.
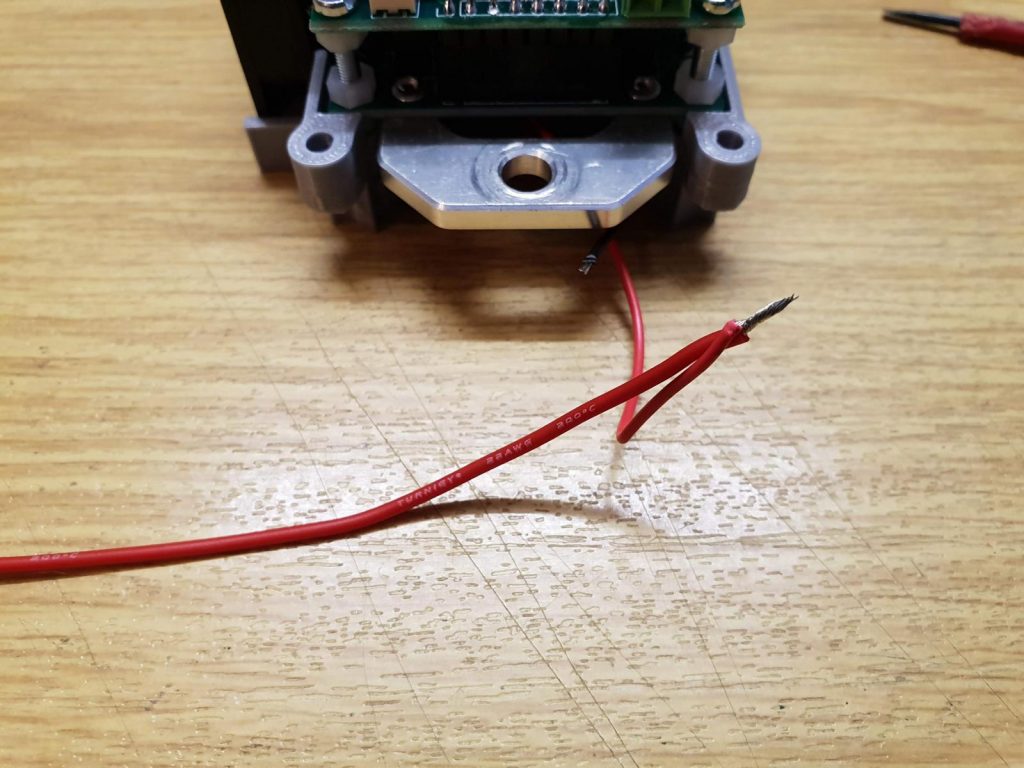
Take the silicone wire you prepared earlier and twist one end of it together with the positive fan cable end.
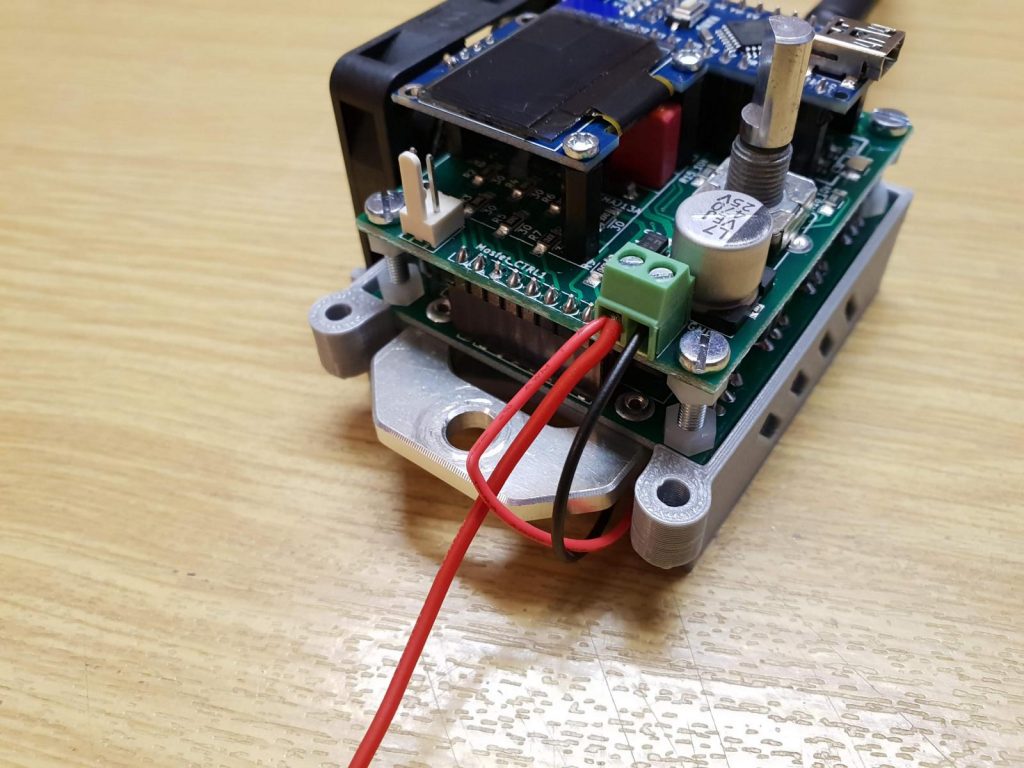
Insert the twisted positive wires and the negative fan wire into the screw terminal.
Take care of the correct polarity. +12V (red wires) is on the left side of the terminal and GND (black wires) on the right side. Polarity is also labeled on the spot welder pcb.
Mounting the case kit to the car battery
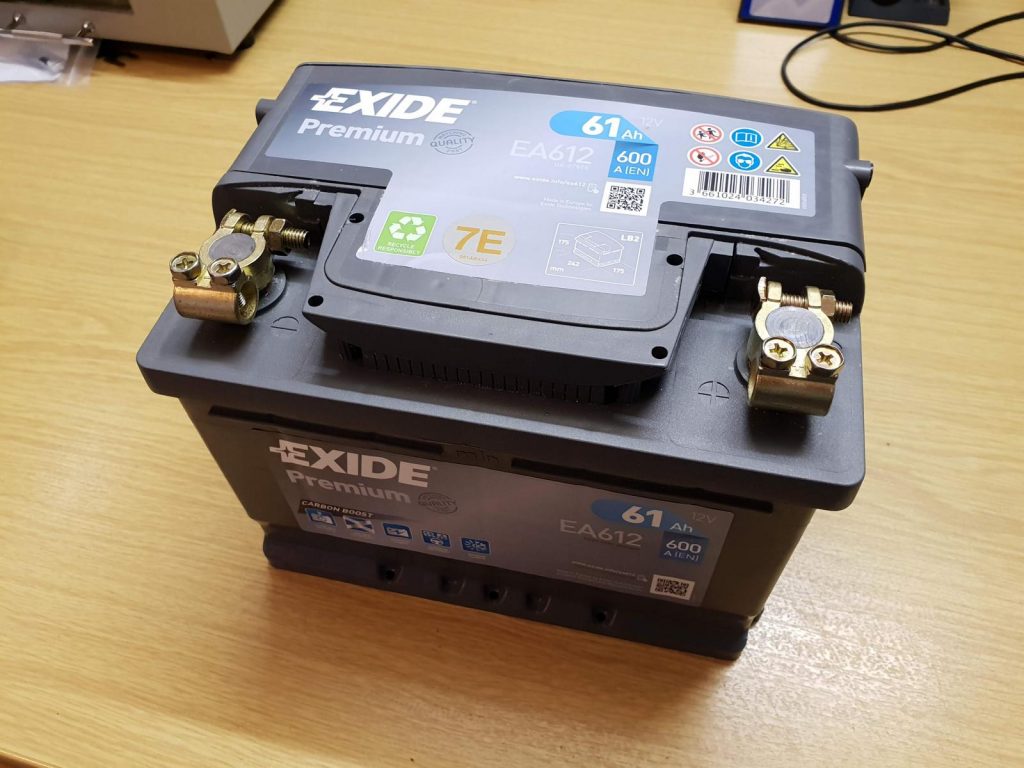
Take your car battery and mount the battery terminals to it.
Important: Please do not connect and use the welder on a car battery that is still installed and connected to your car. Especially not while the car is running. This could cause errors in the car electronics.
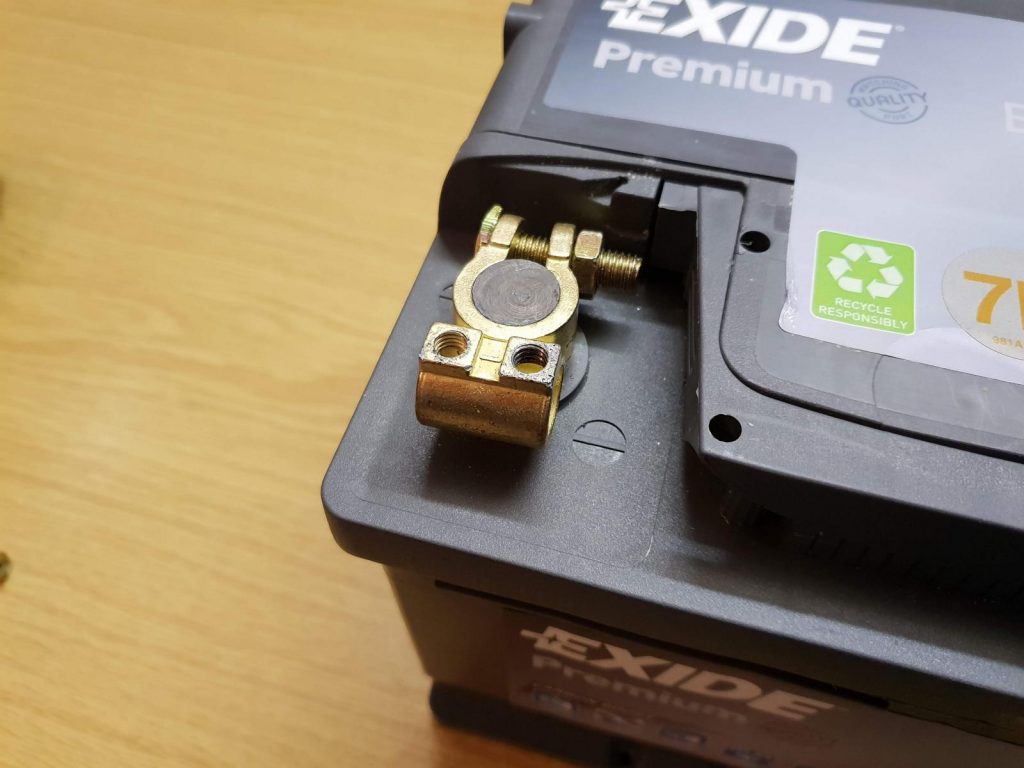
Remove the screws from the negative battery terminal.

Hold the case assembly with one hand and screw the u-shaped aluminium part to the battery terminal.
Make sure you firmly tighten the screw to get a good electrical contact between the battery terminal and the aluminium part.
Also take care that no cables are clamped while tightening the screw.
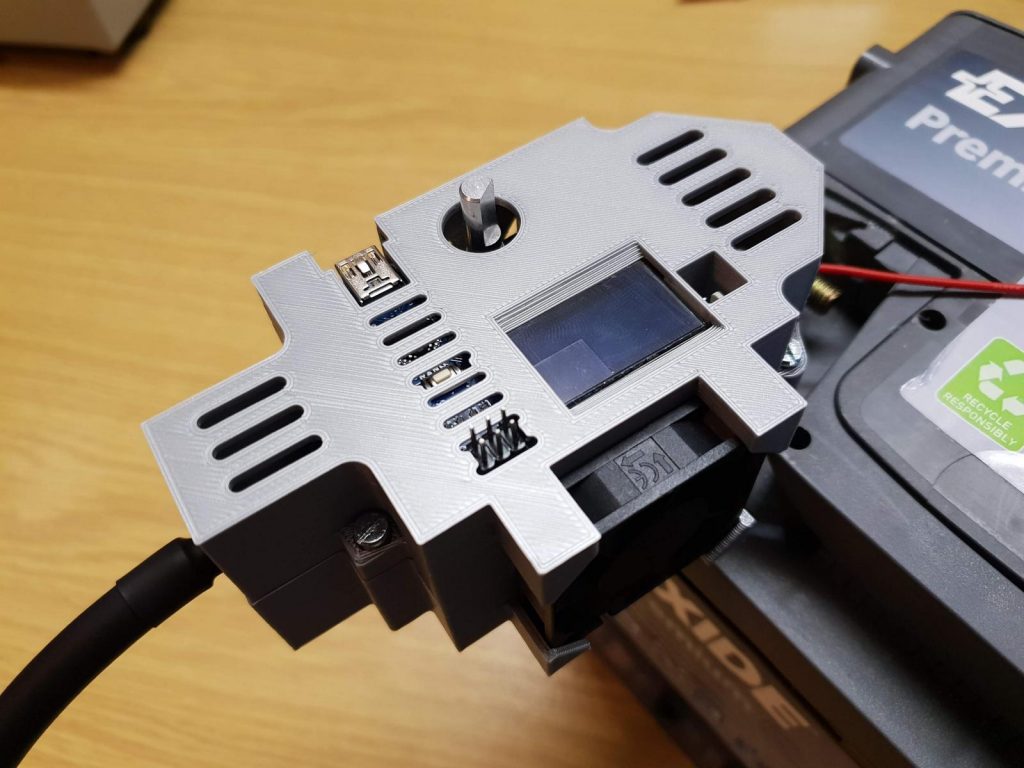
Slide the top half of the case on and secure it with 4 M3x30 screws.
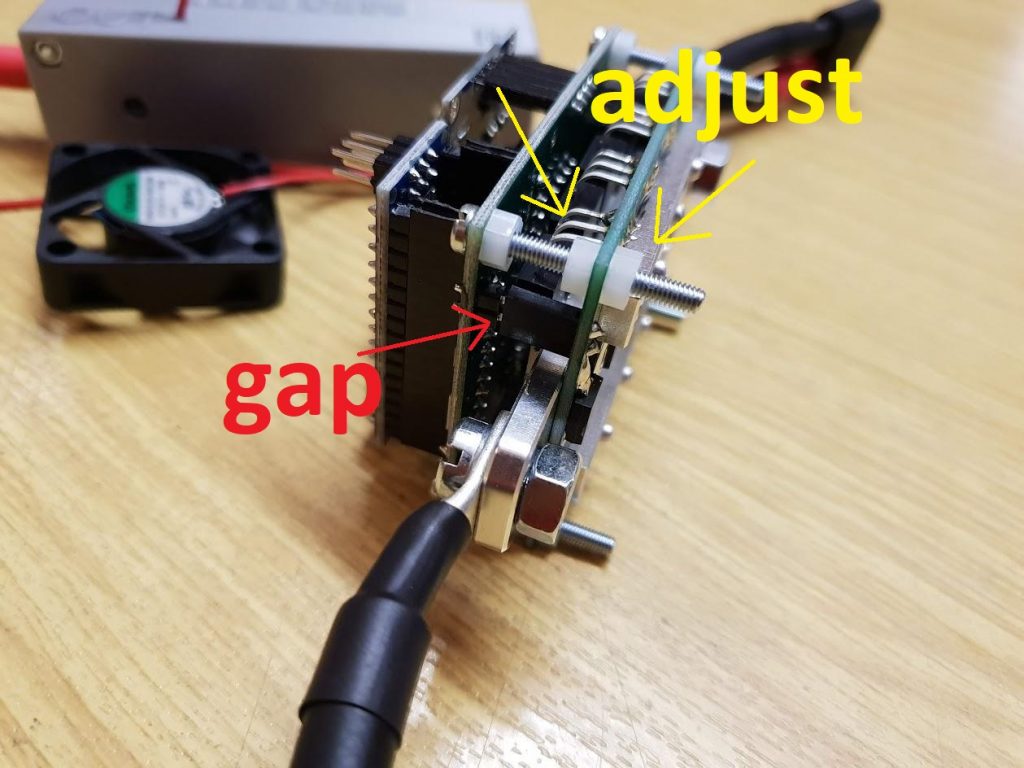
Quick Tip: If the Spot Welder sits to loose in the case you can adjust the distance between the 2 pcbs with the 2 nylon nuts on the bottom pcb.
Just dont put the two pcbs to far apart so the 8-pin and the two 2-pin headers still have good contact. 1 or 2 millimeter gap is ok.
Finally you need to assemble the rotary encoder knob.
When sliding it on the rotary encoder make sure you align it corectly to the rotary encoders shaft. Dont push to hard so you do not damage the rotary encoder or the spot welder pcb.
Tip: Should the knob fit to tight on the rotary encoder heat the 3d printed knob with your hair dryer a bit. Then try to push the warm knob onto the rotary encoder. It should slip on much easier now.
Prepairing the fuse case

For this step you will need the fuse case and its accessory bag.
Insert the M3 Nuts into the 3d printed parts. To do this stick a M3 screw through the hole and screw on a M3 nut.
Tighten the screw to pull the nut into its pocket. Make sure the nut is aligned properly to the pocket when pulling it in.
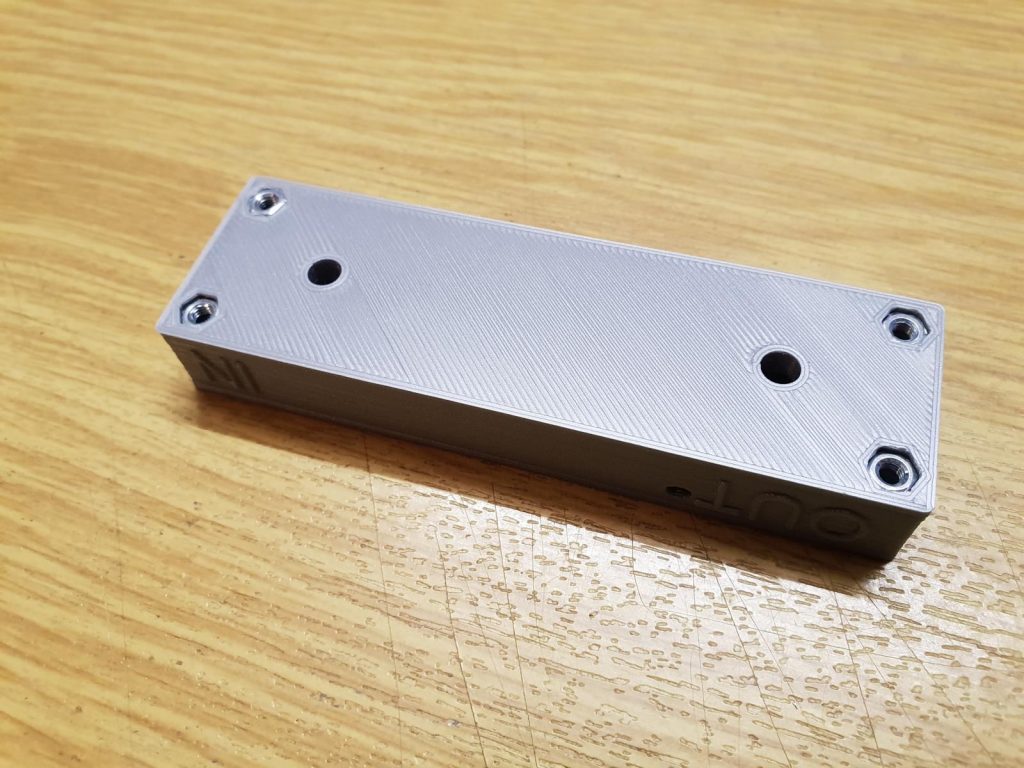
Repeat for all 4 M3 nuts.
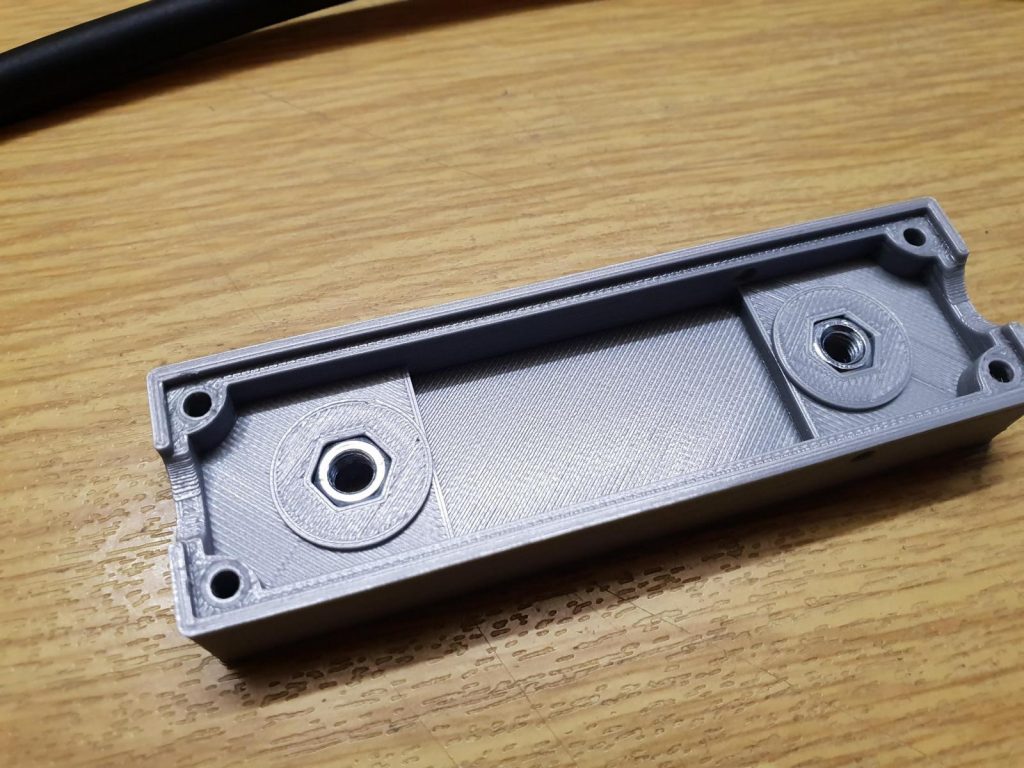
Insert the two M5 nuts into their pockets. They should fit pretty easy. If not use the same method as with the M3 nuts to pull them in.
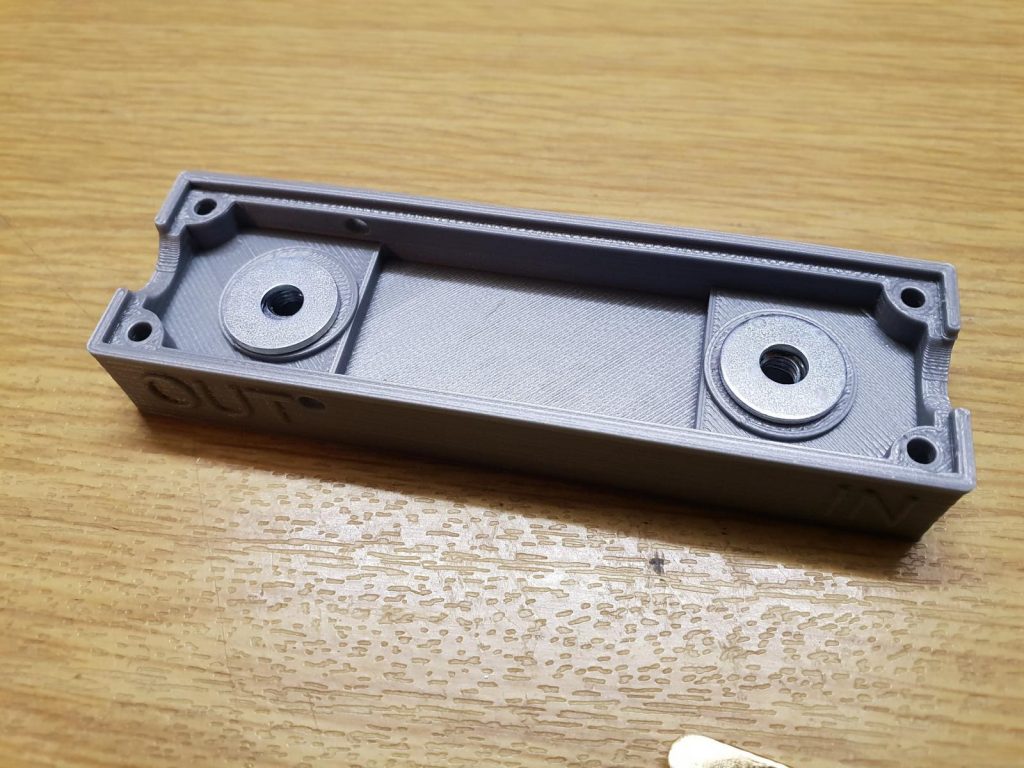
Place the 2 steel washers onto the M5 nuts.
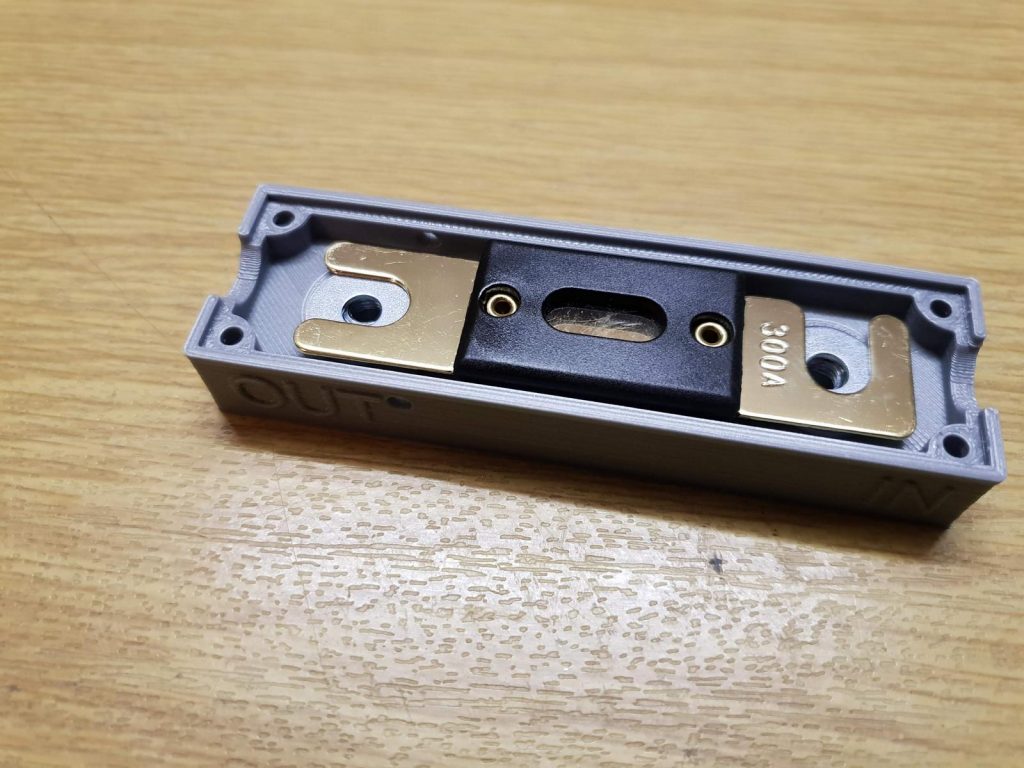
Place the ANL 300A fuse on the washers.
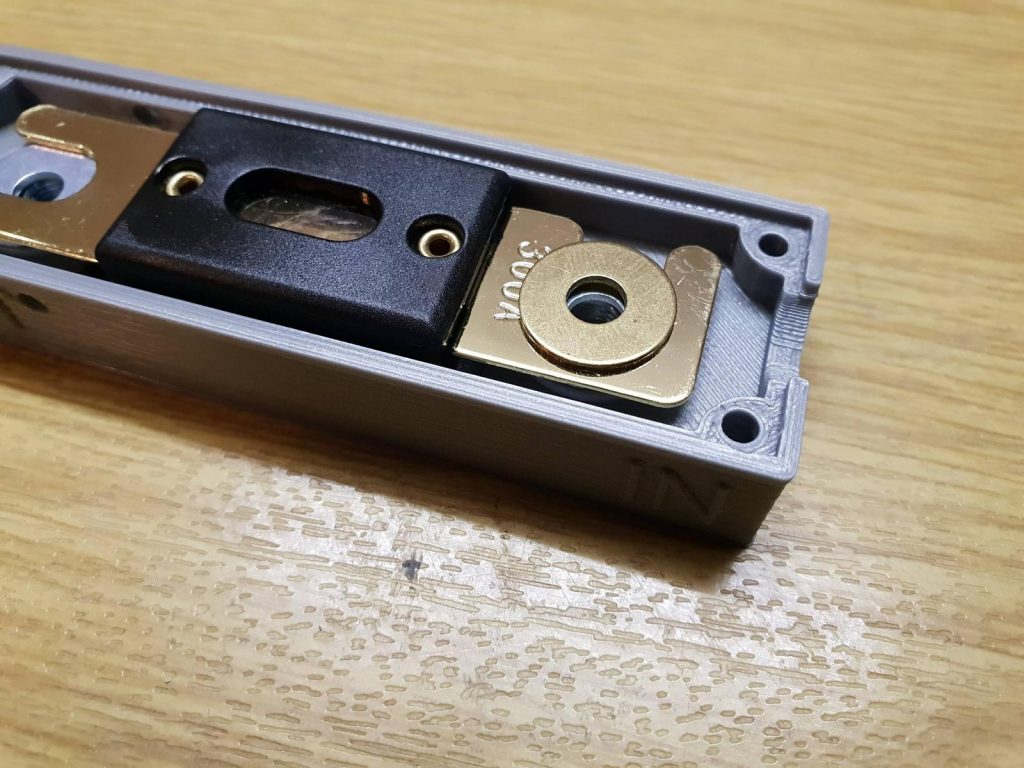
Place one of the brass washers on the side of the fuse case that is labeled “IN” .
It is important to use the brass washer here and not the steel washer because all the welding current will have to go through this washers. Using the steel washers between the welding cable and fuse may decrease welding performance.
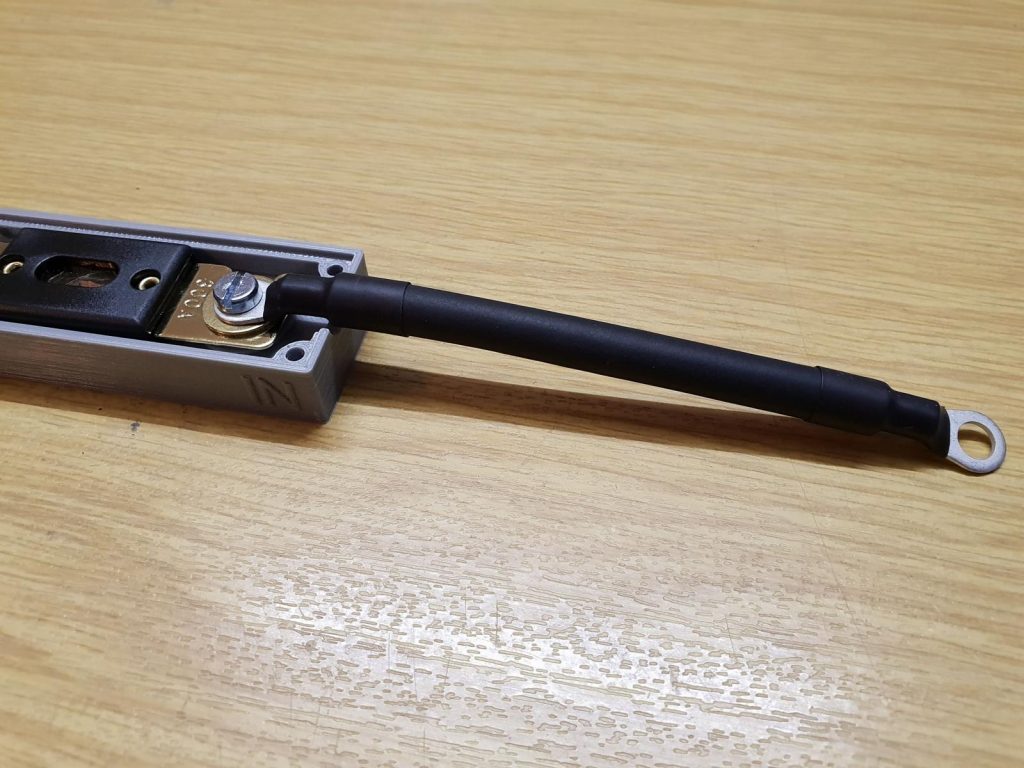
Place the cable shoe of the extension cable on top of the brass washer, put in a M5x12 screw and firmly tighten it.
Mounting the fuse case to the car battery
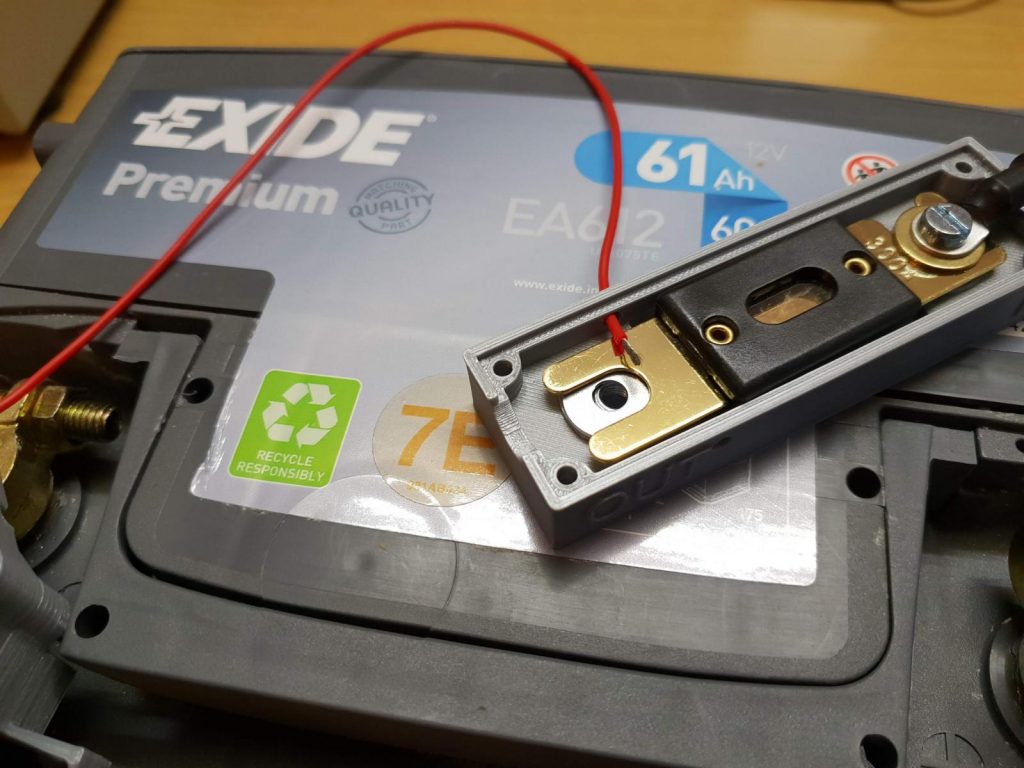
Lay the half assembled fuse case on the car battery and slide the silicone cable from the prebuilt kit through the hole in the side of the fuse case.
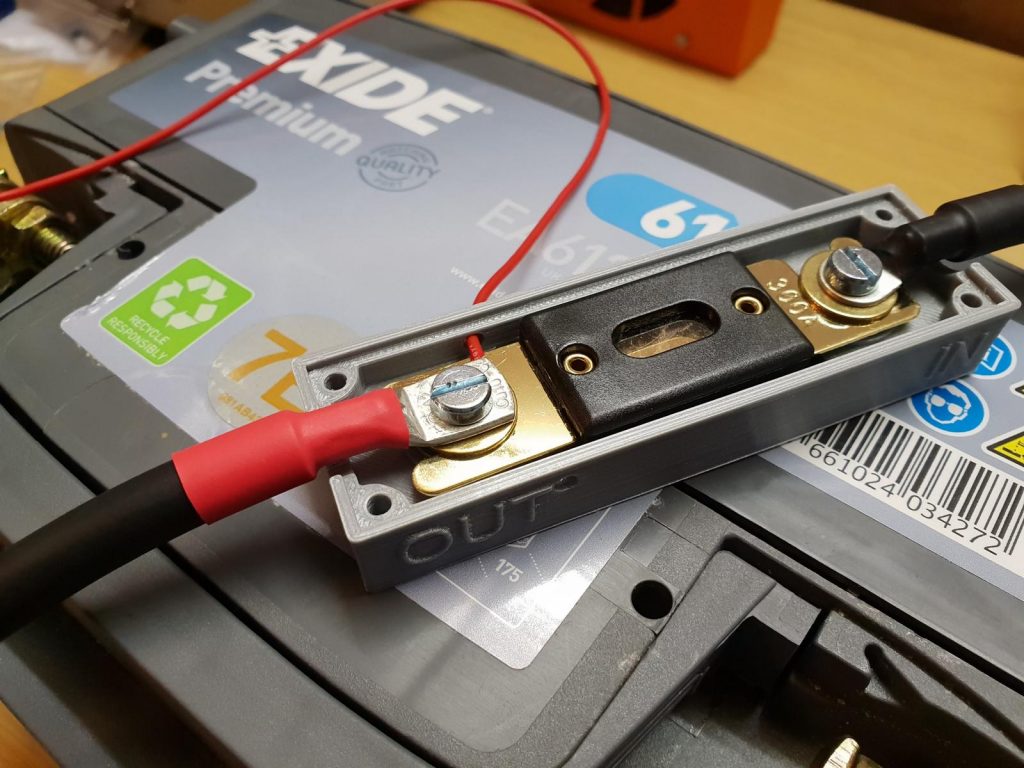
Place a brass washer on the fuse and place the cable shoe of the positive welding cable on top of the brass washer.
Insert the M5x12 screw and tighten it a bit.
Then slide the end of the silicone cable between the washer and the fuse and fully tighten the M5 screw.
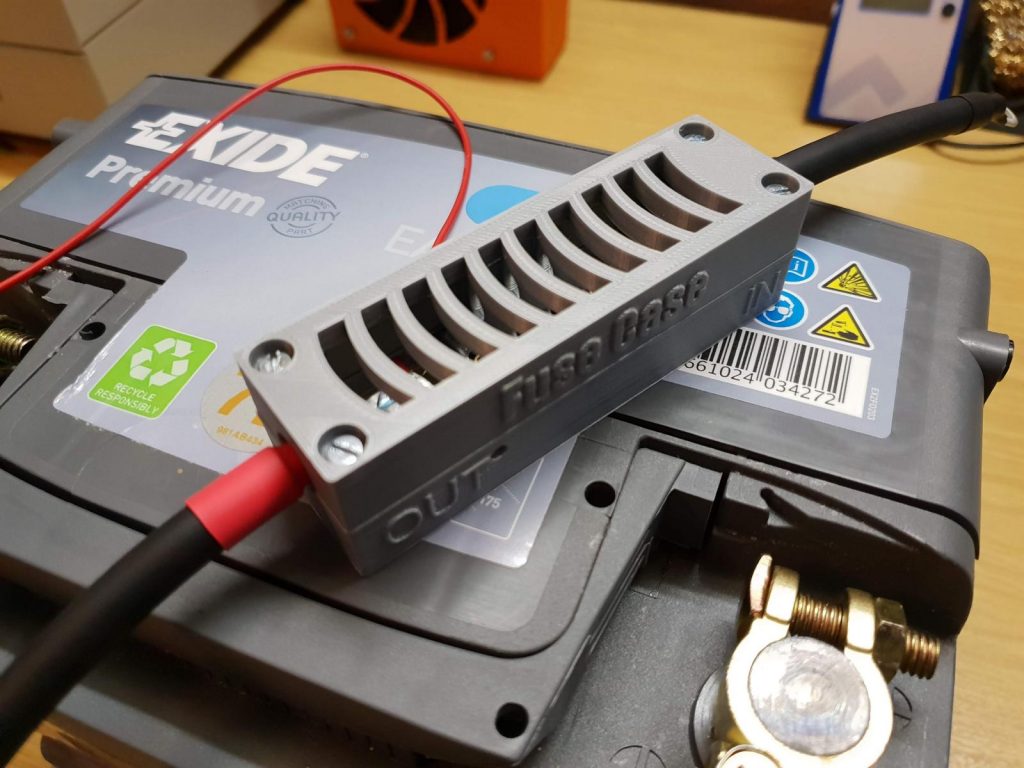
Close the case with the top 3d printed part and secure it with 4 M3x25 screws.
Assembly Finished
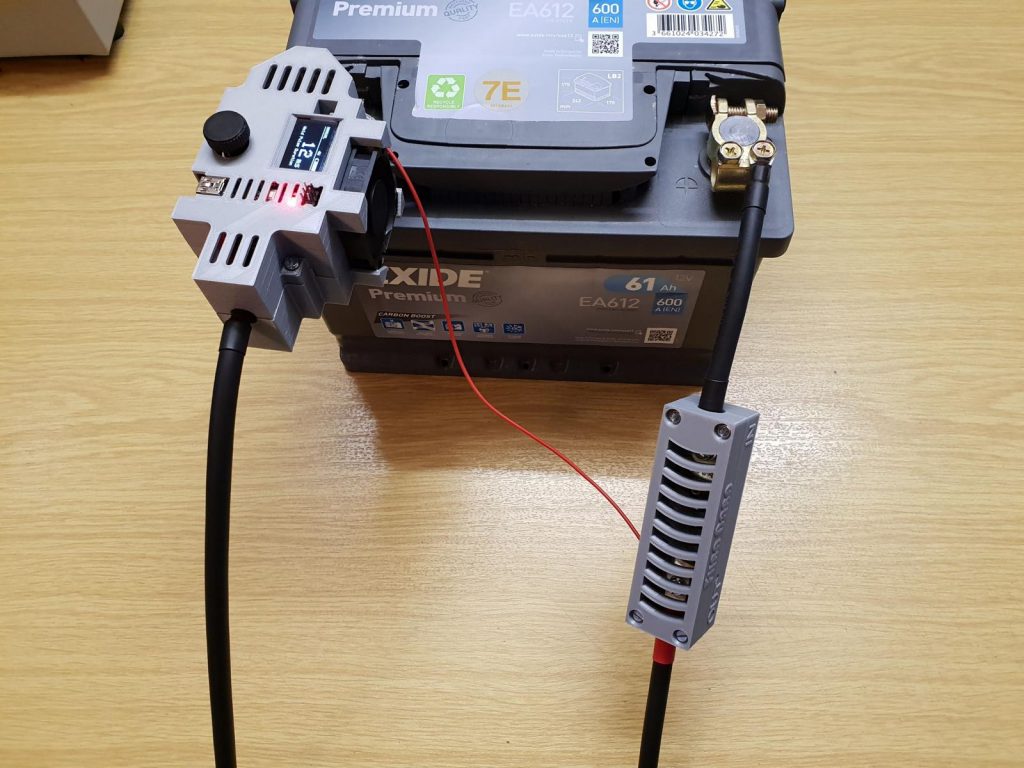
Finally screw the cable shoe of the extension cable to the positive terminal of your car battery. The Spot Welder should start now and is ready to weld.
Before you start welding please also read the Quick Start Guide.
When you are done with the weld job simply unscrew the cable from the positive battery terminal.
It is also possible to add a switch to the red silicone cable to turn the welder on and off. If you do this it is highly recommended to insulate the welding tips with some electrical tape when storing the unit, so they can not accidentally touch something and cause a short circuit.